JPV Concrete Polishing is a South East Melbourne based business specializing in Mechanically Polished Concrete flooring. Established in late 2018, JPV Concrete Polishing services all Melbourne Metropolitan areas, as well as catering to the outer suburbs and country towns. With over 12 years experience in the construction and concrete industry, we can provide quality workmanship at an affordable price.
Within the concrete flooring industry there are a large number of machinery, tooling and treatment products available, JPV Concrete Polishing uses only industry leading machinery, products and tooling to ensure a high quality finish on each and every job.
About Mechanically Polished Concrete:
Mechanically Polished Concrete is a product that is generally suitable for indoor flooring surfaces; it involves diamond grinding the concrete down to the clients desired aggregate exposure, power grouting pinholes and cracks, then scratch removal by further finer diamond tooling and the application of concrete densifiers. This process creates a smooth hardwearing surface, which is then sealed with a high-quality penetrative sealer and a final buff of the surface. Mechanically Polished Concrete does not have a topical coating such as epoxy or polyurethane over the top of the surface. JPV Concrete Polishing offers mechanical polishing on new and old floors, while established floors will dictate colour, aggregate size and aggregate location within the slab, new homes have the option to select colours and aggregates to suit the owner’s preference. New builds are encouraged to approach a concrete polishing contractor prior to any concrete being laid, to ensure a flawless finish.
Aesthetically, Mechanically Polished Concrete offers a sustainable and affordable approach to styling your home or workspace; you have the option to select a variety of aggregate exposure levels and surface finishes such as: honed/matte, low-gloss and high gloss.
Types of Mechanical Polished Concrete JPV Concrete Polishing offers:
Honed
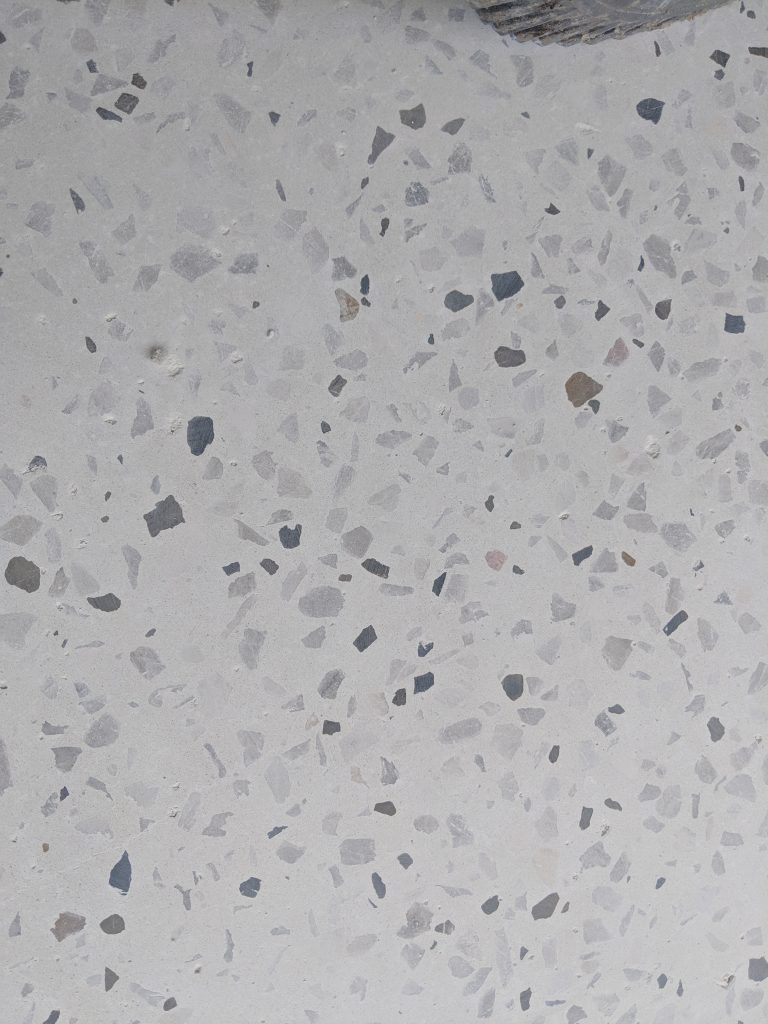
Matte
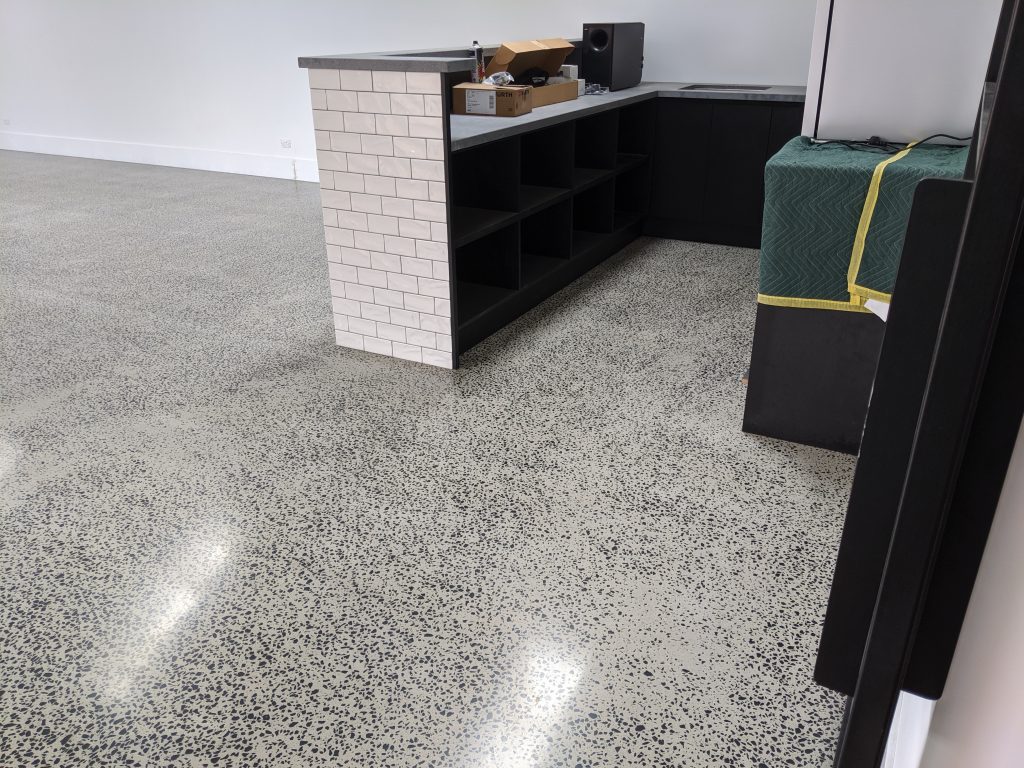
Low-gloss

Mid-Gloss
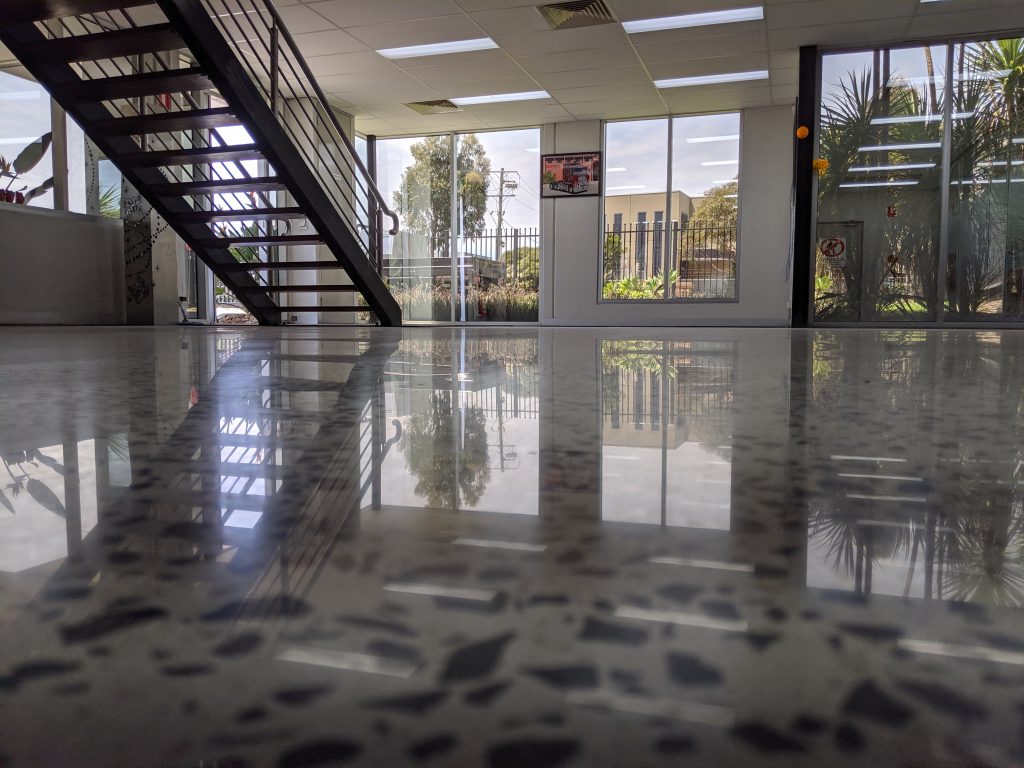
High-Gloss
